The 6 Benefits of Real-Time Equipment Monitoring You Need to Know
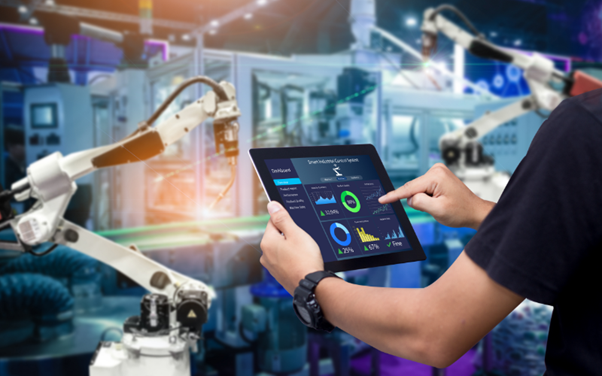
Real-time equipment monitoring has reshaped how industries oversee machine operations, offering unprecedented insights into performance, health, and efficiency. With technology advancing rapidly, machine monitoring and equipment monitoring have become indispensable for businesses aiming to maintain a competitive edge. Here’s a detailed look at six crucial benefits of implementing real-time monitoring systems.
1. Enhancing Operational Efficiency
Real-time monitoring maximises operational efficiency by constantly tracking machine performance metrics. Equipment monitoring systems gather essential data on machine activity, helping operators and managers see where inefficiencies arise and adjust strategies accordingly. By focusing on improving specific areas, businesses can optimise resource allocation and enhance productivity.
Improved efficiency translates into streamlined processes, as data gathered by these systems informs quick decisions without waiting for manual checks. Monitoring solutions also reduce resource wastage, allowing companies to better control costs. Ultimately, operational efficiency supports businesses in achieving goals faster, strengthening productivity, and driving growth.
2. Reducing Unexpected Downtime
Monitoring equipment in real-time significantly lowers the likelihood of unexpected downtime. Equipment breakdowns halt operations, leading to missed deadlines and lost revenue. A monitoring system provides alerts when machine performance dips below-set standards, giving operators time to rectify issues before they escalate.
With predictive maintenance features, equipment monitoring becomes a proactive tool rather than reactive, anticipating potential failures. By taking preventative actions, businesses save time and money, avoiding costly repairs and protecting operational flow. Reducing downtime not only enhances productivity but also builds reliability within a company’s operational framework.
3. Improving Safety and Compliance
Real-time monitoring prioritises safety by identifying potential hazards before they impact employees. Machine monitoring systems offer alerts when specific thresholds are reached, enabling operators to act immediately and prevent accidents. This attention to detail ensures a safer work environment and reduces risks associated with machinery.
Safety compliance is essential in regulated industries, where failing to meet standards could lead to severe penalties. Equipment monitoring helps ensure that machines operate within safe parameters, supporting compliance with legal and industry standards. This approach secures workforce well-being and minimises liabilities for the organisation, making it easier to meet safety requirements consistently.
4. Boosting Decision-Making with Data Insights
Access to real-time data empowers teams to make better decisions quickly. Equipment monitoring systems provide critical information on usage patterns, machine health, and energy consumption, helping managers see the full picture. Armed with this information, teams make informed decisions regarding maintenance, operations, and future equipment investments.
Beyond operational adjustments, these insights support long-term planning. By examining data trends, businesses determine the most effective areas for improvements, budgeting, and scaling. Clear insights allow for smarter allocation of resources, ensuring that time and money are invested in ways that directly benefit the organisation.
ALSO READ: Can Equipment Monitoring And Tracking Improve Profitability?
5. Enhancing Maintenance Planning and Cost Management
Effective maintenance planning becomes more achievable with real-time monitoring. Traditional maintenance schedules often result in unnecessary inspections, which increase expenses without adding value. Conversely, equipment monitoring data highlights when maintenance is needed, enabling precise, on-demand maintenance planning.
This method of managing maintenance keeps machines running at optimal levels while avoiding over-servicing. The financial impact of this improvement is substantial, as maintenance costs decrease, and equipment longevity increases. Predictive maintenance also minimises the frequency of purchasing replacements, saving on capital expenditure while improving asset lifespan.
6. Optimising Energy Usage
Energy efficiency is a primary concern for businesses seeking to reduce operational costs and environmental impact. Machine monitoring helps optimise energy consumption by identifying usage patterns and providing real-time updates on energy-intensive processes. By actively monitoring energy use, companies cut down on unnecessary consumption, conserving resources and lowering utility expenses.
This proactive stance on energy management also aligns with sustainability goals, making equipment monitoring a vital tool for companies prioritising eco-friendly operations. As companies adjust energy practices based on data-driven insights, they reduce their environmental footprint while simultaneously improving profitability—a powerful dual benefit for modern businesses.
Discover how Overdrive IOT can elevate your business with seamless machine and equipment monitoring solutions tailored to your operational needs. Contact Overdrive IOT today to start your journey towards efficient, proactive, and insightful equipment management.